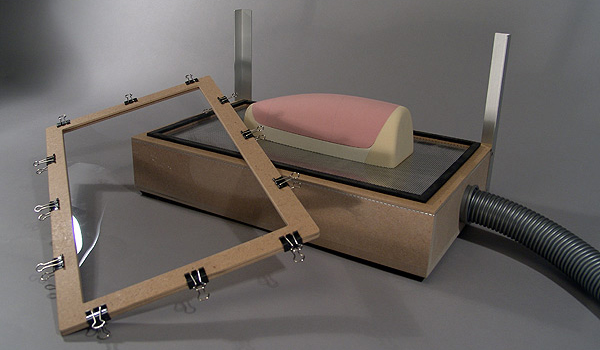
Downloadplan Tiefziehteile selber herstellen
Es gibt viele Stellen an einem Modellflugzeug, an denen wir bevorzugt tiefgezogene Bauteile einsetzen. Spontan fallen mir ein paar Stichworte ein: Kabinenhaube, Motorhaube, Motorattrappen, Pilotenbüsten, Servoabdeckungen, Radschuhe, Randbögen, Spinner und dergleichen.
Insbesondere bei Eigenbauten können Tiefziehteile geradezu das Tüpfelchen auf dem I sein. Wie sieht schon ein vorbildgetreuer Flieger aus, bei dem die Kabinenhaube fehlt? Gut, dann kann man noch immer Modelle mit offenem Cockpit bauen?
Aber fangen wir doch mal ganz klassisch mit der Begriffserklärung an: was sind Tiefziehteile? Eigentlich sprechen wir hier vom Unterdruck-Warmumformverfahren. Eine Kunststoff-Materialgruppe, die sich Thermoplast nennt, lässt sich in einen Rahmen gespannt bei wohldosierter Wärmezufuhr umformen, weil das Material dabei weich wird. Nach dem Erkalten behält es die neu erlangte Form. Vormals einer flachen Folie gleich, wird nun durch Anschmiegen an ein Urmodell eine definierte Dreidimensionalität erreicht. Und damit sich die Folie auch wirklich überall anschmiegt, kann sie durch Luftabsaugen sehr deutlich dazu überredet werden. Damit wäre dann auch der Zusatz „Unterdruck“ erklärt.
Tiefziehbox Marke Eigenbau
Dieser Unterdruck, den wir problemlos mit einem Haushaltsstaubsauger erzeugen, ist der wahre Trick an der Sache. Man kann alternativ auch ohne Unterdruck tiefziehen, und zwar indem man das Urmodell wie ein Stempel möglichst tief ins erwärmte Material eindrückt. Dabei zieht’s sich soweit, dass es sich idealerweise überall anlegt. Aber mit dem Staubsauger macht der Vorgang noch mehr Freude: Die Ergebnisse sind reproduzierbarer und es können viel feinere Details und Konturen abgebildet werden.
Eine einfache Tiefziehvorrichtung – ich nenne sie Tiefziehbox – besteht aus einer kleinen Kiste mit einem Lochblech drauf. Sie hat die Funktion, einen gleichmäßigen Unterdruck zu erzeugen, sobald das erwärmte Material über das Urmodell gestülpt wird. Die Kiste besitzt daher seitlich ein Loch zum Anschluss des Staubsaugers und oben drauf eine umlaufende Dichtung aus Moosgummi.
Das Material selbst spannen wir mit so genannten Mauly-Klemmen aus dem Bürobedarf in einen zweiteiligen Holzrahmen aus glatter Hartfaserplatte. Die anschließende Erwärmung findet im haushaltsüblichen Backofen statt. Hier gilt es allerdings, das Vorhaben mit der Hausdame abzustimmen. Die zwangsläufig freigesetzten Gerüche stoßen nicht immer auf das nötige Verständnis. Dennoch ist der Küchenbackofen ein ideales Gerät für unseren Zweck.
Tiefziehverfahren
Zur Vorbereitung schließen wir den Staubsauger an (noch nicht einschalten) und halten ihn in Reichweite. Die Tiefziehbox steht ebenfalls gut erreichbar über dem Backofen, damit der Weg zwischen Ofen und Box möglichst kurz ist. Der Ofen steht auf voller Temperatur und Oberhitze. Positionieren Sie nun zunächst das Urmodell (zu dessen Bau komme ich im Anschluss) mittig auf das Lochblech. Spannen Sie eine passend vorgeschnittene Folie mit zirka acht Mauly-Klemmen zwischen die Holzrahmen ein. An den Klemmhebeln lässt sich der Rahmen nun wie ein Backblech in die oberste Ofenführung einschieben. Ziehen Sie dazu unbedingt Lederhandschuhe an. Spätestens beim Herausnehmen des Rahmens verbrennt man sich sonst sehr unangenehm die
zarten Finger.
Die eingespannte Folie wird im Ofen die ganze Zeit sehr sorgsam beobachtet, denn nur so erkennt man die richtige Materialtemperatur: Erst wird sich die Folie wellen, dann glättet sie sich allmählich wieder. Daraufhin wird sie beginnen durchzuhängen. Genau dann muss es schnell gehen! Staubsauger an, Ofen auf, Rahmen raus, und von oben zügig, geradlinig und zielstrebig auf die Tiefziehbox-Dichtung ablegen. Dann macht es „Plopp“, und das Teil ist fertig. Dünnere Folien kühlen bereits in zirka zwei bis zehn Sekunden derart ab, dass man den Staubsauger ausschalten kann. Der Rahmen kann entfernt werden, und nach dem Entformen des Urmodells trennen wir nun mit einer Nagelschere das Bauteil entlang der endgültigen Beschnittkontur heraus.
Geeignete Materialien
Nicht jeder Thermoplast ist für unseren Einsatzzweck wirklich geeignet. Zwar ist Acrylglas bekanntermaßen warmumformbar, aber für Modellflug-Bauteile zu spröde. Nach dem Heraustrennen müssten Acrylteile anschließend getempert werden, um keine Spannungsrisse zu bekommen. Ganz klar: da gibt’s Besseres. Auch sollte man die Finger von transparentem Polystyrol lassen, wie es manchmal im Baumarkt als Bastlerglas erhältlich ist. Ganz im Gegensatz zu weiß durchgefärbtem Polystyrol ist das transparente Material nach dem Umformen unwahrscheinlich spröde und kann wie Glas zerbersten. Bloß nicht!
Als nahezu ideal eignen sich für transparente Bauteile Hart-PVC und PET-G. Letzteres ist unter dem Handelsnamen Vivak im Modellbaufachhandel sehr verbreitet und insbesondere in niedrigen Materialstärken ab 0,5 Millimeter (mm) zu bekommen. Hart-PVC gibt’s sogar meist schon sehr preiswert ab 0,2 mm – und dazu noch in vielen transparenten Einfärbungen. Polycarbonat (Makrolon) geht auch, ist aber um ein Vielfaches teurer. Lohnt sich deshalb nicht.
Für nicht-transparente Bauteile ist erneut Hart-PVC eine feine Sache, da die verfügbare Farbpalette meist recht groß ist. Alternativ wären typischerweise weiß durchgefärbtes Polystyrol und ABS zu nennen. Mein Tipp geht aber wieder zum Hart-PVC, allein schon aufgrund der guten Verfügbarkeit bei vielen Händlern sowie dem günstigen Grundpreis.
Das Urmodell
Am Beispiel einer Kabinenhaube soll nun erläutert werden, wie man für ein gegebenes Flugzeug das Urmodell anfertigt. Dazu stellt sich wieder die Materialfrage: Gut geeignet ist ein Klotz aus hartem Balsaholz, den wir in Form sägen, schnitzen, raspeln und schleifen können. Alternative: Lindenholz. Da ist die Oberfläche gleich deutlich härter.
Noch viel besser geeignet ist PUR-Hartschaum, auch Kunststoffblockmaterial genannt. Dies gibt es in unterschiedlichen Dichten und im Anschauungsmodellbau-Fachhandel auch in handlichen Abgabemengen, die Formbarkeit ist wirklich fantastisch. Es lässt sich perfekt spanabhebend bearbeiten und besitzt bei einer Dichte von zirka 600 kg/m³ eine geschlossenzellige Oberfläche, die weder grundiert noch lackiert werden müssen, Feinschliff mit 400er-Schleifpapier genügt. Unter 600 kg/m³ ist das Material zwar leichter zu bearbeiten, aber die Oberfläche wird zunehmend porös und kann sich durchaus bei transparenten Tiefziehteilen unangenehm abbilden. Über 600 kg/m³ hingegen wird’s unangenehm hart, das sollte man sich einfach nicht antun.
Doch zurück zum Bau des Urmodells. Wir fangen einfach an und nehmen uns die Kabinenhaube eines kleineren Segelflugmodells vor. Der Kabinenausschnitt ist bereits gegeben, und damit steht die Seitenkontur schon mal zur Hälfte fest. Die Oberseite des Urmodells erhält dann noch genau die Wölbung, die in der Rumpfkontur notwendig ist. Die komplette Seitenkontur wird also auf einen geeigneten Rohklotz übertragen und möglichst winklig herausgetrennt. Das geht am besten mit einer Bandsäge, ansonsten muss man mit Handwerkzeug ran. Als Zweites folgt die Draufsicht, sodass sich der noch eckige Klotz exakt in die Kabinenöffnung einsetzen lässt. Drittens wird nun derart verrundet, dass wir letztendlich eine passgenaue Vollmaterial-Haube besitzen.
Dieser Haubenrohling ist leider noch nicht bereit für das Tiefziehverfahren, denn er muss noch unterfüttert werden. Hier können wir getrost irgendwelche Materialreste anstückeln, denn alles was wir jetzt hinzubauen, wird ja später am Bauteil abgeschnitten. Es kommt also nicht auf ein paar Klebenähte mehr oder weniger an. Vor dem Unterfüttern schleife ich an die Beschnittkontur des Urmodells eine leichte Fase (zirka 1 × 1 mm) an, damit man diese Kontur später gut erkennen kann, um daran entlang zu schneiden.
Die Unterfütterung hat die wichtige Aufgabe, einen homogenen Übergang des eigentlichen Urmodells zum Boden darzustellen. Sie muss also den Konturverlauf der Urmodell-Oberfläche aufnehmen, damit innerhalb der Beschnittkontur keine Wellen, Blasen oder Zipfel entstehen. Auch ist eine gewisse Gesamthöhe notwendig, da sich das Tiefziehmaterial nicht zwangsläufig eckig an den Boden anschmiegt. Meist entsteht eine Hohlkehle, die in passender Entfernung zur Beschnittkante aber nicht weiter stört.
Hinterschnitte sind zu vermeiden, da man das Urmodell sonst nicht mehr herausbekommt. Deshalb halten wir an allen Seiten eine allgemeine Formschräge ein, je nach Bauteil, aber so zwischen zwei und zehn Grad ist schon nicht schlecht.
Selber machen
Mit etwas Übung hält sich der Aufwand in überschaubaren Grenzen, sobald man sich erst einmal das geeignete Equipment gebaut und Tiefziehmaterial in ausreichender Menge bevorratet hat. Denn auch mit viel Erfahrung kann man nicht ausschließen dass immer mal wieder ein Zug daneben geht, weil man zum Beispiel die Temperatur nicht getroffen hat, oder weil das Urmodell ein dickes Staubkörnchen trug.
Fangen Sie doch mal damit an, sich den Bauplan zur Tiefziehbox aus dem Downloadbereich der FlugModell-Internetseite herunterzuladen – kostenlos natürlich. Der mehrseitige Plan ist in DIN-A4 gehalten und enthält Zeichnungen, Bauanleitung sowie eine Zuschnittliste für Ihren Gang zum Holzfachhandel.